Advancements in Digital Light Processing (DLP) 3D Printing for High-Resolution Prototypes
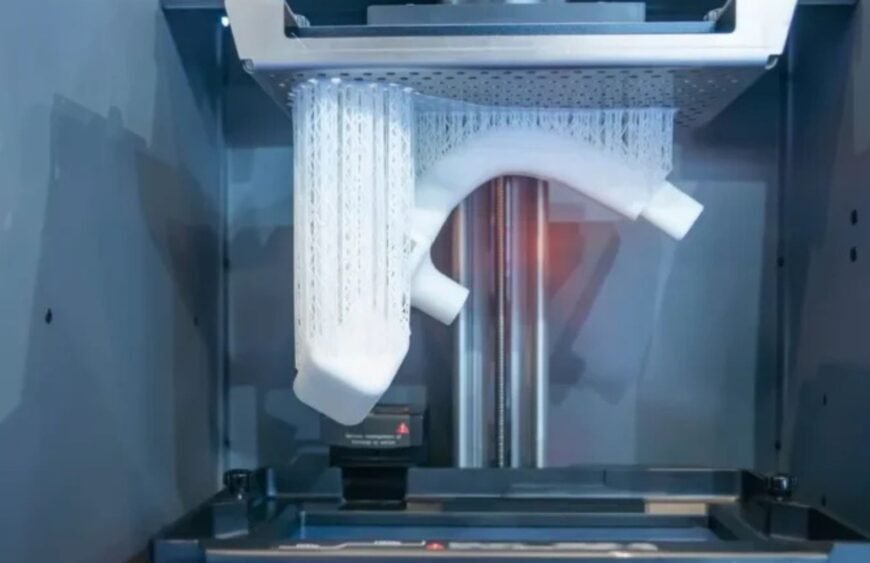
Digital Light Processing (DLP) 3D printing is transforming high-resolution prototyping with its precision, speed, and efficiency. This technology’s ability to produce intricate designs makes it indispensable for industries like healthcare, jewelry, and consumer products.
With advancements in materials, hardware, and software, DLP continues to push the limits of innovation, offering faster workflows and unparalleled detail. In this blog, we’ll explore the latest breakthroughs in DLP technology and their impact on 3D printing services and manufacturing solutions.
What is DLP 3D Printing?
Digital Light Processing 3D Printing is a resin-based additive manufacturing technology that uses light to cure photopolymer materials into solid objects. Unlike traditional 3D printing methods that build objects line by line, DLP uses a digital light projector to cure entire layers simultaneously, significantly speeding up the process.
This method delivers exceptional resolution, making it ideal for creating intricate designs and high-detail prototypes. Compared to similar technologies like Stereolithography (SLA), DLP stands out for its speed and layer uniformity, thanks to its use of a digital micromirror device (DMD). Industries such as healthcare, jewelry, and consumer goods favor DLP for producing precise, functional parts with minimal material waste.
How DLP Technology Works
Digital Light Processing (DLP) 3D printing operates by curing photopolymer resin layer by layer using a projected light source. The process begins with a digital micromirror device (DMD) that reflects UV light onto the resin surface, selectively solidifying the material in precise patterns.
Unlike other methods, such as SLA, DLP cures entire layers at once rather than tracing them line by line, resulting in faster production times. The cured layer is then lifted, allowing fresh resin to flow into place for the next layer.
This layer-by-layer process ensures high resolution, uniformity, and exceptional detail, making DLP ideal for applications requiring intricate geometries and smooth surface finishes. Its speed and accuracy distinguish it as a leader in resin-based 3D printing.
Recent Advancements in DLP Technology
Digital Light Processing (DLP) 3D printing has seen significant advancements that enhance its capabilities for high-resolution prototyping.
- High-Performance Resins: New photopolymer formulations offer improved mechanical strength, flexibility, and biocompatibility, expanding DLP’s application in industries like healthcare and automotive.
- Enhanced Light Sources: Advanced UV projection systems now deliver greater precision, enabling finer details and smoother finishes in complex designs.
- Software Innovations: AI-powered slicing tools and adaptive resolution controls optimize workflows, reducing print times while maintaining exceptional accuracy.
- Real-Time Monitoring: Cloud-based systems now allow for real-time adjustments and improved quality control, ensuring consistency across production runs.
Applications of DLP 3D Printing for High-Resolution Prototypes
Digital Light Processing (DLP) 3D printing has become a go-to technology for creating high-resolution prototypes, meeting the exacting demands of various industries. Its ability to produce detailed, precise, and functional parts has made it indispensable in fields requiring intricate geometries and smooth finishes.
Healthcare:
DLP plays a critical role in medical applications by enabling the creation of surgical guides, dental aligners, hearing aids, and prosthetics. Its biocompatible resins and high-resolution capabilities ensure patient-specific solutions with exceptional accuracy, improving procedural outcomes and patient comfort.
Jewelry and Fashion:
Designers and jewelers leverage DLP for rapid prototyping and production of intricate designs. It allows for the creation of highly detailed pieces, such as engagement rings and fashion accessories, ensuring faster iteration cycles and accurate representations of final products.
Consumer Electronics:
The technology is widely used to prototype small and complex parts, such as casings, connectors, and wearable devices. Its high precision ensures a perfect fit and functionality, enabling manufacturers to validate designs before moving to mass production.
Automotive and Aerospace:
In these sectors, DLP is utilized for creating highly detailed prototypes of parts like engine components, air ducts, and intricate control mechanisms. These prototypes are essential for testing and validating designs under real-world conditions before committing to production.
Education and Research: DLP is increasingly being used in academic and research settings to create precise models for study, experimentation, and teaching. Its accessibility and accuracy make it ideal for fostering innovation and hands-on learning.
Benefits of Using DLP for 3D Printing Services
Digital Light Processing (DLP) 3D printing offers numerous advantages, making it a preferred choice for 3D printing service providers seeking to deliver high-quality results efficiently. Here are the key benefits:
- Unparalleled Speed: Unlike traditional layer-by-layer methods, DLP cures entire layers simultaneously using projected light. This significantly reduces production times, allowing service providers to meet tight deadlines without compromising quality.
- Exceptional Detail and Precision: DLP’s ability to achieve ultra-fine resolutions makes it ideal for intricate designs and detailed prototypes. Industries requiring high precision, such as healthcare and jewelry, benefit greatly from this capability.
- Cost-Effectiveness: The simultaneous layer curing process minimizes resin waste and optimizes material usage, making DLP a cost-efficient option for service providers.
- Versatile Material Options: With advancements in photopolymer resins, DLP supports a wide range of materials, including those with properties like flexibility, strength, and biocompatibility. This versatility allows service providers to cater to diverse industry needs.
- Superior Surface Finish: DLP delivers smooth surface finishes, reducing the need for extensive post-processing. This saves time and effort, enabling faster delivery to clients.
- Scalability and Customization: DLP systems are suitable for producing both single prototypes and larger batches of customized parts, providing flexibility for small-scale and high-volume projects.
Future of DLP 3D Printing
The future of Digital Light Processing (DLP) 3D printing is set to bring transformative advancements:
- AI Integration: Smarter workflows with optimized slicing and issue prediction.
- Sustainable Resins: Development of biodegradable and eco-friendly materials.
- Multi-Material Capabilities: Printing complex parts with diverse material properties.
- Enhanced Hardware: Faster, higher-resolution systems for improved efficiency.
- Industry 4.0 Integration: Cloud connectivity and real-time monitoring for smart factories.
- Broader Applications: Expansion into aerospace, medical implants, and advanced electronics.
Conclusion
DLP 3D printing is revolutionizing high-resolution prototyping with its precision, speed, and efficiency. Its advancements in materials and technology continue to drive innovation across industries. By adopting DLP, businesses can achieve superior prototypes and stay competitive in evolving markets. Discover how Tesseract’s DLP services can bring your designs to life with exceptional quality and speed.